About Us
About Us
At Quality Screw Machine Products, our dedication to precision, consistency, and reliability is rooted in our team of highly skilled professionals. Every member of our setup personnel brings over 10 years of experience in the trade, ensuring expert craftsmanship and attention to detail in every job. This wealth of knowledge allows us to deliver complex, tight-tolerance parts with unmatched accuracy, no matter the scale of the project.
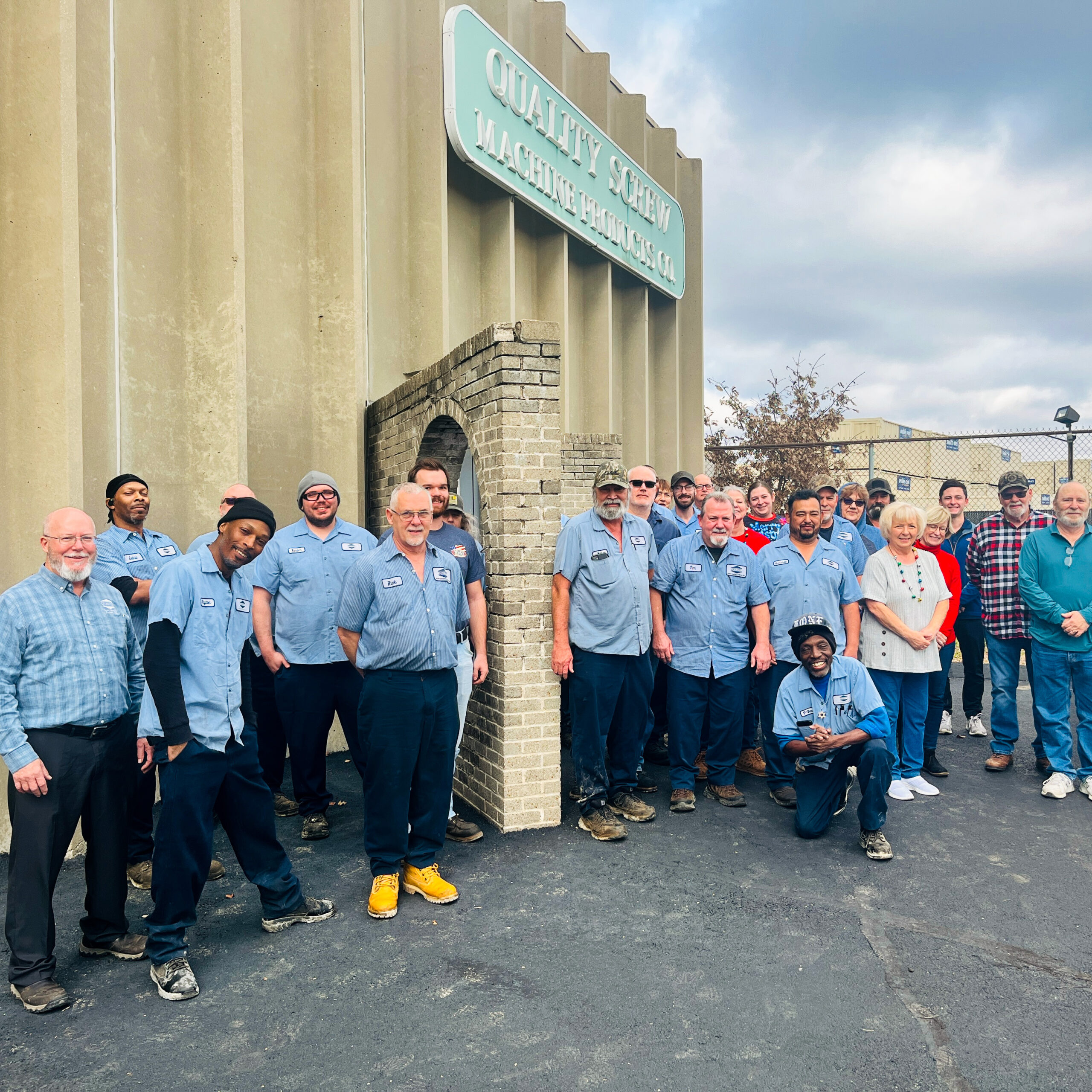
Our History
Founded in 1987, Quality Screw Machine Products has grown from humble beginnings into a leading provider of precision-machined components. Originally established in a 5,000-square-foot facility in St. Louis, our company focused on producing low-volume, high-quality parts. Today, our commitment to excellence has fueled continuous growth, and we now operate from a 33,000-square-foot facility, equipped with advanced machinery and technology to meet the evolving demands of modern manufacturing.
Over the years, our company has evolved from a small operation into a versatile, full-service machining partner. While we have expanded our production capabilities to accommodate higher volumes and more complex projects, we have never lost sight of the core values that built our reputation: quality, reliability, and customer satisfaction. We continue to invest in the latest technology, such as CNC lathes, Swiss turning machines, and vertical milling centers, to provide our clients with the best possible solutions for their manufacturing needs.
Our Clients
Our clients span a variety of industries, including automotive, aerospace, medical, agriculture, and more. Whether it’s producing high-precision components for life-saving medical devices, rugged parts for heavy equipment, or intricate automotive support systems, we are proud to deliver parts that consistently exceed industry standards.
Our Commitment
As we look to the future, Quality Screw Machine Products remains committed to growing alongside our clients. We will continue to expand our capabilities, refine our processes, and uphold the values that have guided us since our founding. Our team is ready to tackle any challenge, providing the expertise and precision that define every part we produce.
Thank you for considering Quality Screw Machine Products as your trusted machining partner. We look forward to supporting your business with the highest level of craftsmanship and service.
Our Quality Policy
The Management and Employees of Quality Screw Machine Products commit themselves to the pursuit of excellence by exceeding our customers’ expectations for world-class products and service every day.
Inspection
Our inspection department is equipped with essential tools to ensure precise quality assurance and measurement. Our optical comparator allows for detailed visual inspection of parts. Our profilometer accurately gages surface roughness and texture. We have an a Dimensionair, air gage system that provides highly sensitive measurement of internal bores, ensuring tight tolerances. In addition, we utilize a range of handheld tools, including micrometers, calipers, ring gages, plug gages, pin gages and concentricity gage to verify concentricity with exceptional accuracy, as well as other essential gages. Together, these instruments enable us to verify products meet the highest standards of precision and quality.
Our Certifications
Quality Screw Machine Products, Inc. is certified ISO 9001-2015. FM 678694. British Standards Institution auditors determined the company meets International Organization for Standardization requirements for consistently high-quality products and manufacturing processes.
Screw Machining FAQs
On a daily basis, we receive several similar questions that seem to come up repeatedly from our customers and purchasing agents. So we’ve decided to answers those frequently asked questions most received: